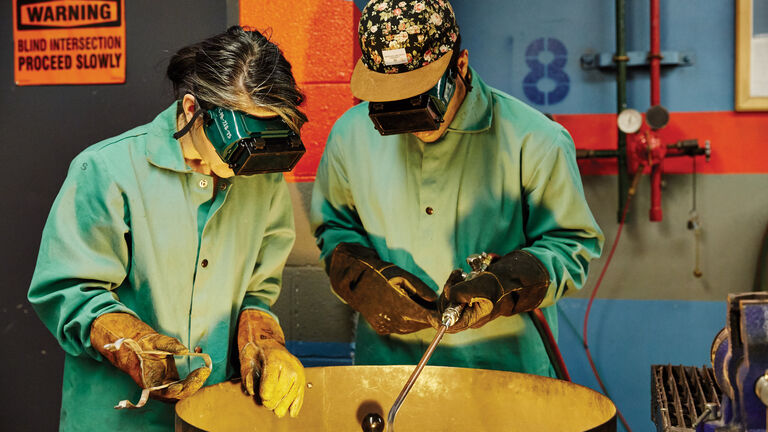
Environmental Health
Environmental Health
SAIC’s Environmental Health and Safety (EHS) team provides a host of programs and services for the SAIC community, including: training, ergonomic assessments, incident investigations, management of regulated waste streams, air quality surveys, hazard assessments, and art project consultation. These programs and services reduce institutional risk, establish safe and healthy work conditions, and promote environmental stewardship. Our mission is to create a community in which environmental, health, and safety principles are accepted, executed, and integrated into all aspects of working, teaching, learning, and living at SAIC.
Injury and Illness Reporting
Faculty must complete the Instructor’s Report for injuries involving students within four hours of the injury or as soon as possible. Return form to IRFM—Environmental Health and Safety.
-
- Report injuries and illnesses to your supervisor immediately following the incident or as soon as possible.
- If your supervisor is not available, report the incident to another supervisor or manager in your department.
- If medical attention is needed, complete the Medical Authorization Form and proceed to Concentra at 1230 West Lake Street, Chicago, Illinois 60607. 312.666.0028.
- Contact Concentra for transportation.
- Return any medical documentation (i.e., work restrictions, return to work notices) to Human Resources—Records.
-
- Facilitate the provision of medical care as needed.
- Complete the Supervisor Report Form and deliver it to Human Resources— Records within four hours of the incident or as soon as possible. If your supervisor is not available, report the incident to another supervisor or manager in your department.
- Notify the Associate Director Environmental Health and Safety for the museum at 312.443.3928 or school at 312.499.4924.
- Any witnesses to the incident should provide written statements and attach them to the injury report.
- Actively work with Environmental Health and Safety to investigate the accident and implement loss prevention measures.
-
- Report all injuries and illnesses to campus security or your instructor immediately.
- If medical attention is needed, proceed to the following locations for medical treatment:
Health Services
Lakeview Building
116 S. Michigan Ave., 13th floor
312.499.4280
Michigan Ave. Immediate Care
180 N. Michigan Ave., suite 1605
312.201.1234
Northwestern Emergency Room
250 E. Erie St.
312.926.2000
Instructional Resources & Facilities Management
Lakeview Building
116 S. Michigan Ave., 15th floor
Vice President of Campus Operations
Tom Buechele tbuechele@saic.edu